In today’s world, proper training for cleaning personnel is more critical than ever. The pandemic underscored the importance of effective cleaning and disinfection practices in reducing the spread of infectious diseases. Ensuring that cleaning staff are well-trained – particularly around infection prevention and proper disinfection protocols – protects public health, enhances the efficiency of cleaning operations, and extends the life of facilities.
This article explores the key aspects of proper cleaning personnel training, including the difference between cleaning and disinfecting, the safe use of disinfectants, personal protective equipment (PPE), updated cleaning protocols, and the adoption of new technologies like electrolyzed water solutions and microfiber tools.
Cleaning vs. Disinfecting: Understanding the Difference
One of the fundamental concepts that cleaning personnel must grasp is the difference between cleaning and disinfecting. These two terms are often used interchangeably, but they serve very distinct purposes:
- Cleaning: The removal of visible dirt, debris, and organic matter from surfaces. It helps reduce the number of germs but does not necessarily kill them.
- Disinfecting: The process of using chemicals to eliminate pathogens on surfaces, significantly reducing the risk of infection.
Proper training ensures that personnel understand when each method is necessary and how to apply them correctly. For example, high-touch surfaces such as doorknobs, handrails, and light switches require regular disinfection in addition to routine cleaning.
Safe Use of Disinfectants
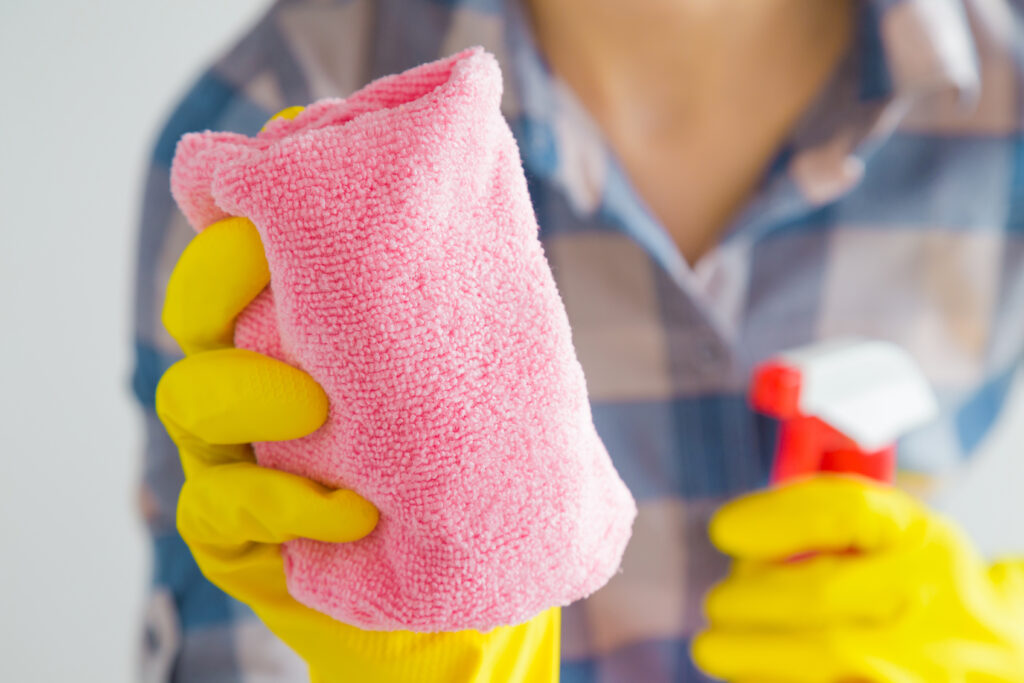
The safe and effective use of disinfectants is crucial in ensuring both human health and environmental safety. Training programs should cover the following areas:
- Proper Dilution: Many disinfectants require dilution to be effective. Over-diluting can render them ineffective, while under-diluting can lead to excessive exposure to harsh chemicals.
- Dwell Time: Every disinfectant has a recommended contact time to be effective. Cleaning staff should be trained to ensure surfaces remain wet for the required duration.
- Avoiding Cross-Contamination: Using separate cloths, mops, or wipes for different areas (e.g., restrooms vs. common areas) and for different surfaces (e.g. faucets vs. light switches) helps prevent the spread of germs.
- Ventilation: Many disinfectants release fumes that can be hazardous if used in poorly ventilated areas. Proper training can help reduce the risk of respiratory issues among staff.
- Storage and Disposal: Disinfectants must be stored safely and disposed of according to regulations to prevent environmental harm and accidental exposure.
Personal Protective Equipment (PPE) and Its Importance
Proper use of PPE is essential for protecting cleaning personnel from hazardous substances and potential infections. Training should include:
- Types of PPE: Gloves, masks, goggles, and gowns are commonly used depending on the task at hand.
- Proper Donning and Doffing: Employees should be trained on the correct sequence of putting on and removing PPE to avoid contamination.
- PPE Maintenance: Understanding when to replace or disinfect PPE is critical in ensuring ongoing protection.
- Compliance with OSHA Guidelines: Staff should be aware of relevant regulations and standards to maintain workplace safety.
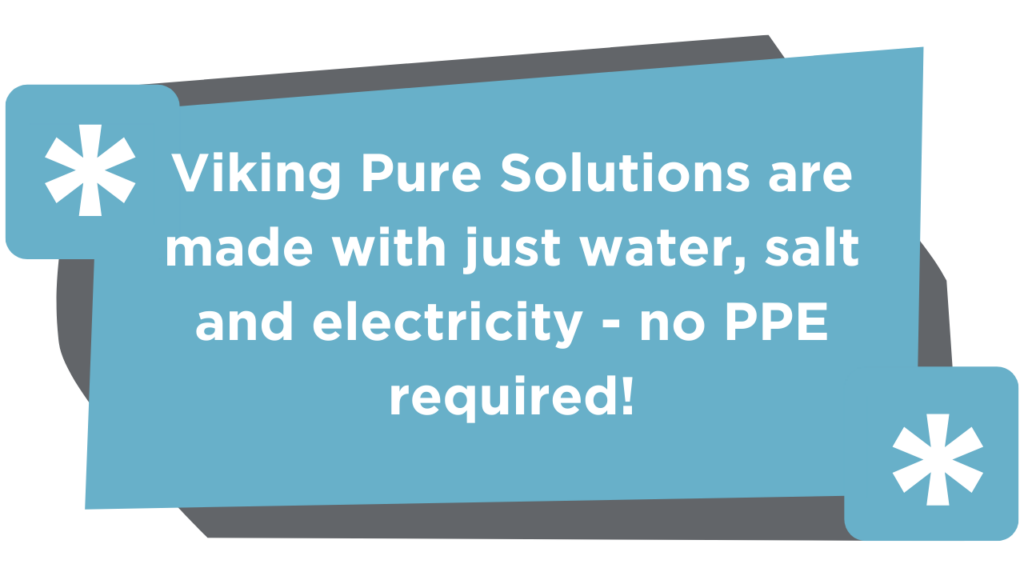
Updated Cleaning Protocols and Best Practices
Cleaning protocols continue to evolve as new research and technologies emerge. Proper training helps personnel stay updated on:
- Frequency of Cleaning: High-traffic areas require more frequent cleaning and disinfection.
- Use of Color-Coded Systems: Many facilities implement color-coded cleaning tools (e.g., red for restrooms, blue for general surfaces, etc.) to prevent cross-contamination.
- Documentation and Reporting: Keeping logs of cleaning schedules, chemical usage, and incidents ensures accountability and helps improve processes.
- Response to Outbreaks: Cleaning personnel should be trained in emergency protocols for outbreaks of contagious diseases.
Training on New Cleaning Technologies
With the advancement of cleaning technologies, staff must be continuously trained to utilize them effectively. Some key innovations include:
Electrolyzed Water Solutions
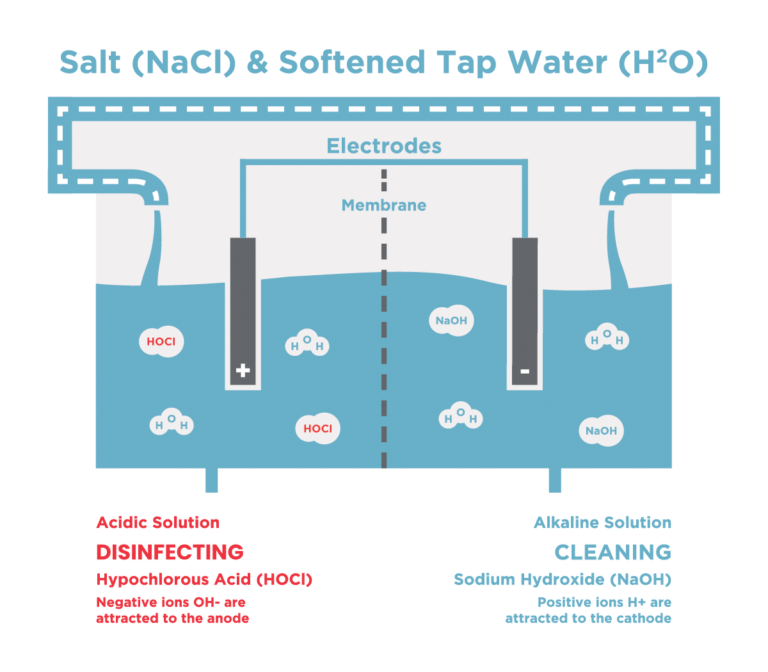
A safer and more environmentally friendly alternative to traditional chemicals, electrolyzed water is produced by passing an electrical current through a saltwater solution, creating a powerful yet non-toxic disinfectant and a multi-purpose cleaning solution. Unlike conventional cleaning products, electrolyzed water solutions do not have a smell, which may initially be surprising to cleaning personnel. Training should emphasize that the absence of fragrance is beneficial, as many fragrances contain volatile organic compounds (VOCs) that can be harmful.
Additionally, in certain situations, such as cleaning bathrooms and handling bodily fluids, personnel should be trained to use electrolyzed water solutions in tandem—first applying the cleaner to remove soil and then following up with the disinfectant to eliminate any remaining pathogens on the surface. Understanding this two-step process is crucial for maintaining hygiene and preventing the spread of infections.
Finally, not all electrolyzed water solutions are the same. Generation systems produce e-water solutions with varying potency in terms of pH and parts per million. It’s important that your team understands how to test the solutions they are using to ensure that the cleaning and disinfecting solutions are the correct potency.
Microfiber Technology
Microfiber cloths and mops are highly effective at trapping dirt and pathogens compared to traditional materials. Unlike cotton or disposable cloths, microfiber contains thousands of tiny fibers that create a larger surface area for capturing dust, dirt, and bacteria. The positively charged fibers attract negatively charged dust and microbes, effectively lifting them from surfaces without the need for harsh chemicals.
Additionally, microfiber can absorb up to six times its weight in water, reducing streaks and improving overall cleaning efficiency.
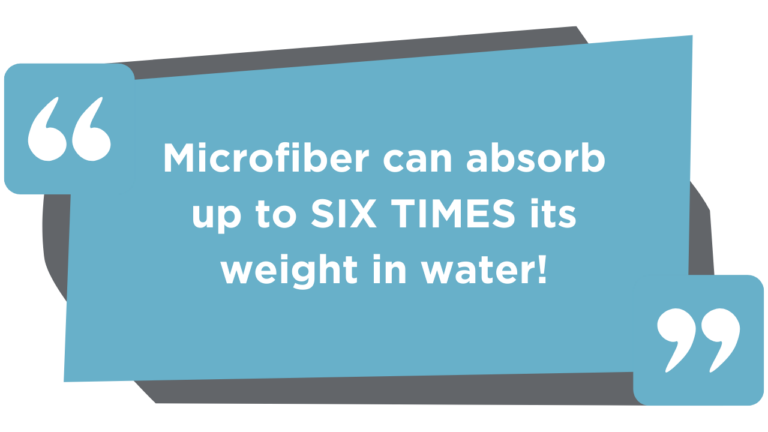
One thing to keep in mind is that microfiber cloths are available in a wide range in terms of quality and function, so it’s important that your cleaning personnel are using the correct material for the job at hand, and that they know the difference between them. Training should cover the proper care and laundering of microfiber tools to maintain their efficacy and prevent cross-contamination.
Automated Cleaning Systems
Robotics and autonomous cleaning machines are becoming more prevalent, requiring specialized training for operation and maintenance. These systems, including robotic vacuum cleaners, autonomous scrubbers, and UV disinfection robots, can enhance cleaning efficiency and reduce labor costs. Cleaning staff should be trained to program, operate, and troubleshoot these machines, ensuring they function optimally.
Additionally, understanding when to supplement automated cleaning with manual intervention is crucial to maintaining high standards of hygiene and sanitation.
LEARN MORE: Using Viking Pure Cleaner in Your Auto Scrubber
Methods for Training and Educating Staff
To ensure cleaning personnel are well-trained, organizations should implement a combination of training methods, including:
- Hands-On Demonstrations: Practical training sessions allow staff to practice proper techniques under supervision.
- E-Learning Modules: Online training courses provide flexibility and allow employees to learn at their own pace.
- Shadowing Experienced Staff: Pairing new hires with experienced personnel fosters mentorship and knowledge transfer.
- Regular Refresher Courses: Continuous education ensures staff remain informed about updates in best practices and new technologies.
- Certification Programs: Encouraging employees to earn industry-recognized certifications enhances credibility and skill levels.
- Feedback and Assessments: Regular performance evaluations and feedback sessions help reinforce learning and identify areas for improvement.
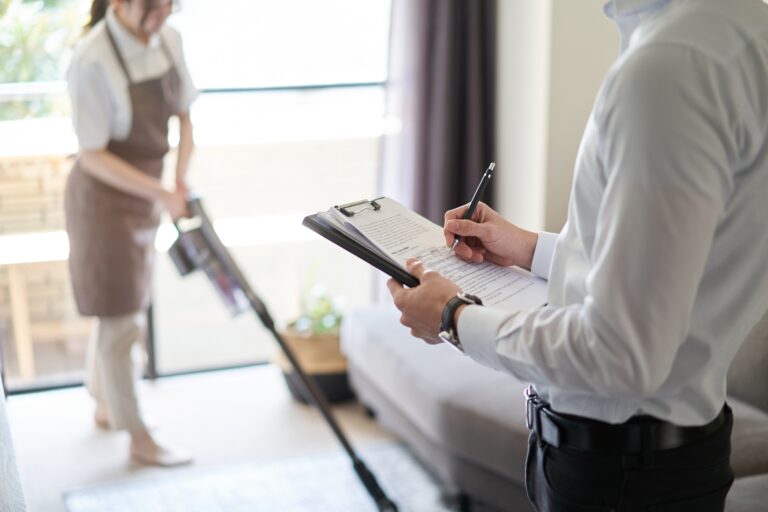
Proper training for cleaning personnel is a cornerstone of maintaining safe, healthy, and efficient environments. By understanding the difference between cleaning and disinfecting, safely using disinfectants, adhering to PPE guidelines, following updated cleaning protocols, and embracing new technologies, cleaning staff can perform their duties effectively and safely.
Implementing comprehensive training programs not only protects the health of employees and building occupants but also improves the overall quality and longevity of facilities. Investing in education and continuous learning is essential in adapting to the ever-evolving landscape of cleaning and sanitation best practices.